نقش مستربچ در رنگسازی چیست
مستربچ (Masterbatch) یکی از مواد مهم در صنایع مختلف به ویژه صنعت رنگسازی و تولید محصولات پلاستیکی است که به عنوان یک افزودنی برای بهبود خواص فیزیکی، شیمیایی و ظاهری محصولات استفاده میشود. مستربچ بهصورت گرانولهای حاوی رنگدانهها، افزودنیها یا پرکنندهها تولید میشود که با رزین پایه ترکیب شده و ویژگیهای خاصی مانند رنگ، مقاومت در برابر UV، یا خواص مکانیکی را به محصول نهایی اضافه میکند. در صنعت رنگسازی، مستربچ به دلیل توانایی در ایجاد رنگهای یکنواخت، کاهش هزینهها و بهبود فرآیند تولید، نقش مهمی ایفا میکند. این مقاله به بررسی این که نقش مستربچ در رنگسازی چیست ؟ انواع آن، فرآیند تولید، مزایا، چالشها و کاربردهای آن در صنایع مختلف میپردازد.
مستربچ چیست
مستربچ ترکیبی غلیظ از رنگدانهها (پیگمنتها)، افزودنیها یا پرکنندهها است که در یک رزین پایه (مانند پلیاتیلن، پلیپروپیلن یا پلیاستایرن) پراکنده شده و بهصورت گرانول عرضه میشود. این ماده بهعنوان یک واسطه در فرآیند تولید محصولات پلاستیکی و رنگآمیزی استفاده میشود. به دلیل غلظت بالای رنگدانهها یا افزودنیها، مستربچ امکان توزیع یکنواخت مواد فعال را در محصول نهایی فراهم میکند و از مشکلات مرتبط با استفاده مستقیم از پیگمنتهای پودری، مانند پراکندگی نامناسب یا تجمع ذرات، جلوگیری میکند.
در صنعت رنگسازی، مستربچهای رنگی (Color Masterbatch) به طور خاص برای افزودن رنگ به محصولات پلاستیکی، فیلمها، الیاف و سایر مواد پلیمری استفاده میشوند. این مستربچها معمولاً شامل رنگدانههای آلی یا معدنی، رزین حامل و افزودنیهایی مانند تثبیتکنندههای UV یا مواد ضداکسیدان هستند.
نقش مستربچ در رنگسازی
مستربچ (Masterbatch) در صنعت رنگسازی نقشی کلیدی ایفا میکند و به عنوان یک افزودنی مؤثر برای رنگآمیزی محصولات پلاستیکی و پلیمری استفاده میشود. این ماده که بهصورت گرانولهای حاوی رنگدانهها، رزین پایه و افزودنیها تولید میشود، امکان ایجاد رنگهای یکنواخت، پایدار و باکیفیت را فراهم میکند و از مشکلات پراکندگی نامناسب پیگمنت پودری جلوگیری مینماید. مستربچ با کاهش نیاز به استفاده مستقیم از رنگدانهها، هزینه های تولید را کاهش داده و فرآیند ترکیب مواد را سادهتر میکند. همچنین، انعطافپذیری در فرمولاسیون، امکان سفارشیسازی رنگها و افزودن خواصی مانند مقاومت در برابر UV یا حرارت را به محصولات میدهد. این ویژگیها به ویژه در صنایعی مانند بستهبندی، خودروسازی و تولید محصولات مصرفی اهمیت دارند. علاوه بر این، مستربچهای سازگار با استانداردهای زیستمحیطی مانند استانداردهای FDA، در کاربردهای حساس مانند بسته بندی مواد غذایی استفاده میشوند. با وجود چالشهایی مانند هزینه اولیه تولید یا نیاز به سازگاری با رزین پایه، مزایای مستربچ از جمله سهولت استفاده و کاهش ضایعات، آن را به ابزاری ضروری در رنگسازی مدرن تبدیل کرده است و انتظار میرود کاربرد آن در آینده گسترش یابد.
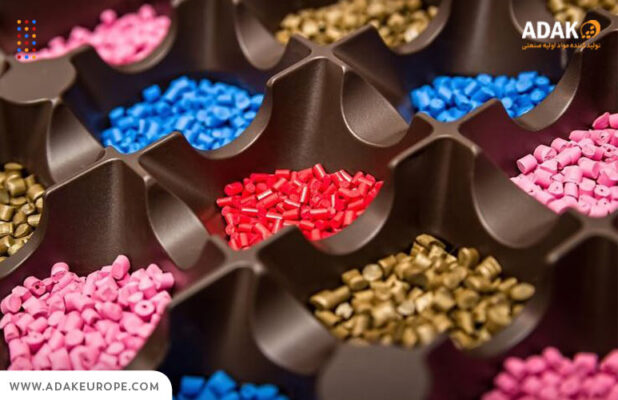
انواع مستربچ های مورد استفاده در رنگسازی
- مستربچ سفید: حاوی تیتانیوم دیاکسید (TiO2) است که برای ایجاد رنگ سفید و افزایش کدری (opacity) در محصولات پلاستیکی استفاده میشود. این نوع مستربچ در صنایع بستهبندی، فیلمهای کشاورزی و تولید لولهها کاربرد دارد.
- مستربچ رنگی: شامل رنگدانههای آلی یا معدنی برای ایجاد رنگهای متنوع است. این مستربچها در تولید اسباببازیها، ظروف پلاستیکی و محصولات تزئینی استفاده میشوند.
- مستربچ مشکی: حاوی کربن سیاه (Carbon Black) برای ایجاد رنگ مشکی و محافظت در برابر UV است. این نوع مستربچ در تولید لولهها و فیلمهای کشاورزی کاربرد دارد.
- مستربچ افزودنی: علاوه بر رنگ، ویژگیهایی مانند مقاومت در برابر UV، خاصیت ضدمیکروبی یا ضدشعله را به محصول اضافه میکند.
فرآیند تولید مستربچ
فرآیند تولید مستربچ شامل مراحل دقیق و کنترلشدهای است که برای اطمینان از کیفیت و یکنواختی محصول نهایی طراحی شدهاند. این فرآیند به شرح زیر است:
- انتخاب و آمادهسازی مواد اولیه:
اولین مرحله، انتخاب مواد اولیه باکیفیت است. این مواد شامل رزین پایه (مانند پلیاتیلن، پلیپروپیلن یا پلیاستایرن)، رنگدانهها (آلی یا معدنی مانند تیتانیوم دیاکسید یا کربن سیاه)، افزودنیها (مانند تثبیتکنندههای UV، روانکنندهها یا مواد ضداکسیدان) و در برخی موارد پرکنندهها (مانند کربنات کلسیم) هستند. انتخاب رزین پایه باید با رزین مورداستفاده در محصول نهایی سازگار باشد تا از مشکلات پراکندگی یا کاهش خواص مکانیکی جلوگیری شود. مواد اولیه معمولاً بهصورت پودر یا گرانول بوده و باید از نظر خلوص و اندازه ذرات بررسی شوند.
- توزین و مخلوط کردن اولیه:
مواد اولیه با دقت توزین شده و در نسبتهای مشخص (بر اساس فرمولاسیون موردنظر) وارد میکسرهای با سرعت بالا یا میکسرهای تخصصی میشوند. این مرحله برای اطمینان از پراکندگی یکنواخت رنگدانهها و افزودنیها در رزین پایه حیاتی است. میکسرها معمولاً مجهز به سیستمهای گرمایش یا خنککننده هستند تا دمای مخلوط را کنترل کنند و از تخریب مواد حساس به حرارت جلوگیری شود. مدتزمان مخلوط کردن و سرعت میکسر به نوع مواد و خواص موردنظر بستگی دارد.
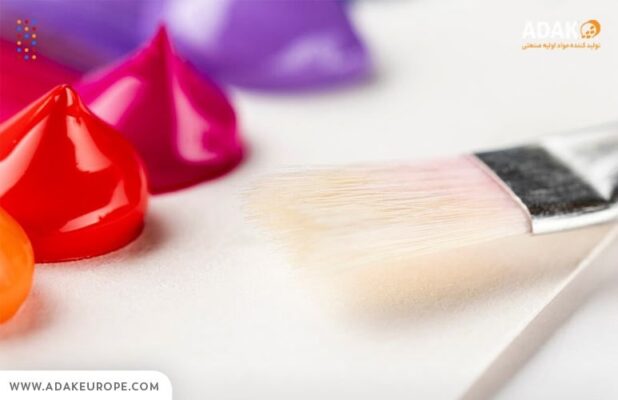
- ذوب و پراکندگی (اکستروژن):
پس از مخلوط کردن اولیه، مواد به دستگاه اکسترودر منتقل میشوند. اکسترودر معمولاً از نوع دوپیچه (Twin-Screw Extruder) است که برای پراکندگی بهتر مواد طراحی شده است. در این مرحله، مخلوط در دمای بالا (معمولاً بین ۱۵۰ تا ۳۰۰ درجه سانتیگراد، بسته به نوع رزین) ذوب شده و تحت فشار و برش مکانیکی قرار میگیرد. این فرآیند باعث پراکندگی یکنواخت رنگدانهها و افزودنیها در رزین پایه میشود. طراحی پیچهای اکسترودر و تنظیم دما و سرعت آن برای جلوگیری از تخریب رنگدانهها یا رزین بسیار مهم است. خروجی اکسترودر بهصورت رشتههای مذاب پلاستیکی است.
- خنکسازی و گرانولسازی:
رشتههای مذاب خارجشده از اکسترودر بلافاصله وارد سیستم خنککننده (معمولاً حمام آب یا سیستم خنککننده هوا) میشوند تا جامد شوند. پس از خنک شدن، این رشتهها توسط دستگاه برش (Pelletizer) به گرانولهای کوچک با اندازه یکنواخت (معمولاً ۲ تا ۳ میلیمتر) تبدیل میشوند. این گرانولها شکل نهایی مستربچ هستند و برای استفاده در فرآیندهای بعدی آماده میشوند.
- کنترل کیفیت و بستهبندی:
در مرحله نهایی، مستربچ تولیدی تحت آزمایشهای کنترل کیفیت قرار میگیرد. این آزمایشها شامل بررسی پراکندگی رنگدانهها، ثبات رنگی، خواص مکانیکی، مقاومت حرارتی و سازگاری با رزین پایه است. ابزارهایی مانند طیفسنجی، میکروسکوپ الکترونی و تستهای رئولوژیکی برای ارزیابی کیفیت استفاده میشوند. پس از تأیید کیفیت، گرانولها خشک شده، در کیسههای مقاوم در برابر رطوبت بستهبندی شده و برای ارسال به مشتریان آماده میشوند.
مزایای استفاده از مستربچ در رنگسازی
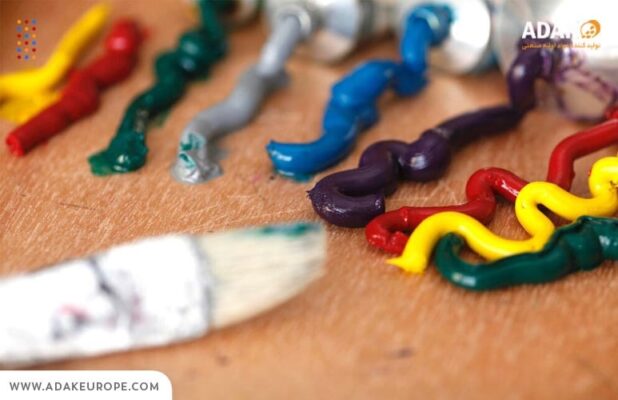
مستربچ بهصورت گرانول عرضه میشود و بهراحتی با رزینهای پایه ترکیب میشود که کاربری آن را بسیار ساده میکند. رنگهای حاصل از مستربچ از پایداری بالایی برخوردارند و در برابر نور، حرارت و مواد شیمیایی مقاومت خوبی نشان میدهند. همچنین به دلیل پراکندگی یکنواخت مواد رنگی، میزان ضایعات ناشی از رنگآمیزی ناهمگن کاهش مییابد. مستربچ امکان تولید طیف گستردهای از رنگها و خواص مختلف را فراهم میآورد و به این ترتیب پاسخگوی نیازهای متنوع در صنایع گوناگون میباشد.
چالشهای استفاده از مستربچ در رنگسازی
در بررسی نقش مستربچ در رنگسازی چیست باید بدانید که استفاده از مستربچ با چالشهایی همراه است. هزینه اولیه تولید مستربچ باکیفیت بالاست، زیرا نیازمند تجهیزات پیشرفته و مواد اولیه گرانقیمت میباشد. همچنین، انتخاب رزین حامل مناسب اهمیت زیادی دارد تا از بروز مشکلات سازگاری با رزین پایه جلوگیری شود. محدودیتهایی نیز در دستیابی به برخی رنگهای خاص وجود دارد که به دلیل محدودیتهای شیمیایی یا حرارتی رنگدانه رخ میدهد. علاوه بر این، استفاده از مستربچ در مقادیر زیاد میتواند خواص مکانیکی محصول نهایی را تحتتأثیر قرار داده و کیفیت فیزیکی آن را کاهش دهد.
کاربردهای مستربچ در صنایع مختلف
مستربچ در صنایع مختلف کاربردهای گستردهای دارد. در صنعت بستهبندی، برای تولید فیلمهای پلاستیکی، بطریها و ظروف رنگی مقاوم استفاده میشود. در خودروسازی، مستربچ به ساخت قطعات داخلی و خارجی با رنگهای پایدار و مقاوم در برابر اشعه UV کمک میکند. صنعت ساختمان نیز از مستربچ برای تولید لولهها، پروفیلها و پوششهای رنگی بهره میبرد. در بخش کشاورزی، مستربچ در تولید فیلمهای گلخانهای و مالچ با خواص UV و رنگهای خاص نقش مهمی دارد. همچنین در محصولات مصرفی مانند اسباببازیها، لوازمخانگی و ظروف پلاستیکی کاربرد فراوانی دارد.
نتیجه گیری
نقش مستربچ در رنگسازی چیست ؟ مستربچ به عنوان یک فناوری پیشرفته در صنعت رنگسازی، نقش مهمی در بهبود کیفیت، کاهش هزینهها و افزایش انعطاف پذیری محصولات پلاستیکی دارد. فرآیند تولید مستربچ، با مراحل دقیق انتخاب مواد، مخلوط کردن، اکستروژن و کنترل کیفیت، تضمینکننده تولید محصولی باکیفیت و یکنواخت است. با توانایی ایجاد رنگهای یکنواخت، پایدار و مقاوم، مستربچها به تولیدکنندگان امکان میدهند محصولاتی با ظاهر جذاب و خواص بهبودیافته تولید کنند. نوآوریهای اخیر، مانند مستربچهای زیستتخریبپذیر و نانوکامپوزیتی، نشاندهنده پتانسیل بالای این فناوری برای پاسخگویی به نیازهای صنایع مدرن است.